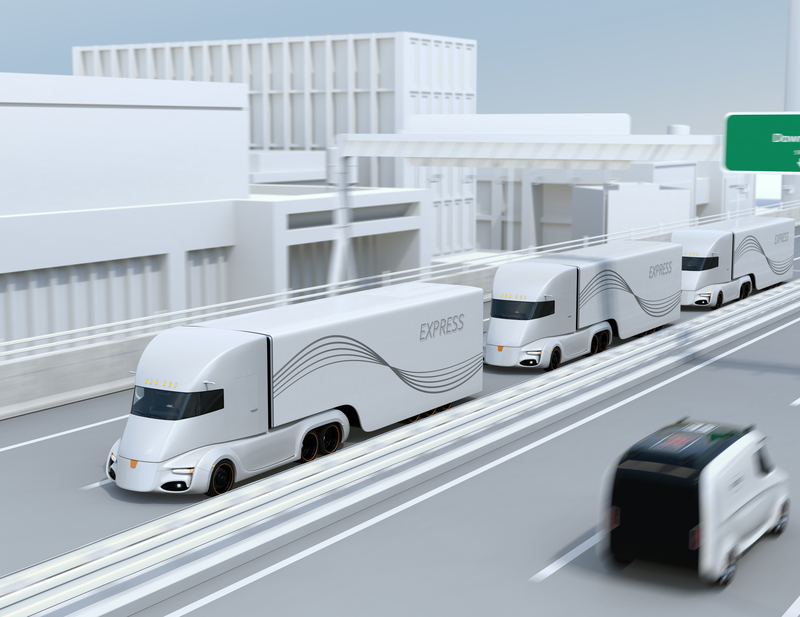
As trials of platooning in live commercial operating environments gather momentum around the world, key value for money issues are emerging around the realistic timescale for wide-scale deployment of the technology. One is the need for more precise quantification than has previously been available of expected fuel (and, in turn, accident) savings. Another concerns the levels of participation that can be expected across the haulage industry as a whole. A third – perhaps the most fundamental - is the need for a legal and financially sound framework for cooperation between the hauliers that are involved in platooning.
Previous, typically off-road studies of the first issue have generated wide variations in the levels of economies that can be expected - not least because of the variety of platooning configurations that have been modelled. In the US, the California Partners for Advanced Transportation Technology (PATH) project indicated savings of 20% for platoons of four or more vehicles - and of up to 30% for longer ones. The European Union (EU)’s Safe Road Trains for the Environment (SARTRE) initiative postulated benefits of up to 8% for the lead vehicle and up to 16% for following ones. The European Automobile Manufacturers Association (ACEA) suggests cuts for the leading vehicle of 8% and of the trailing ones by up to 16%.
Real conditions
Much clearer results are now being expected from current projects that are trialling platooning in real-life operational conditions.
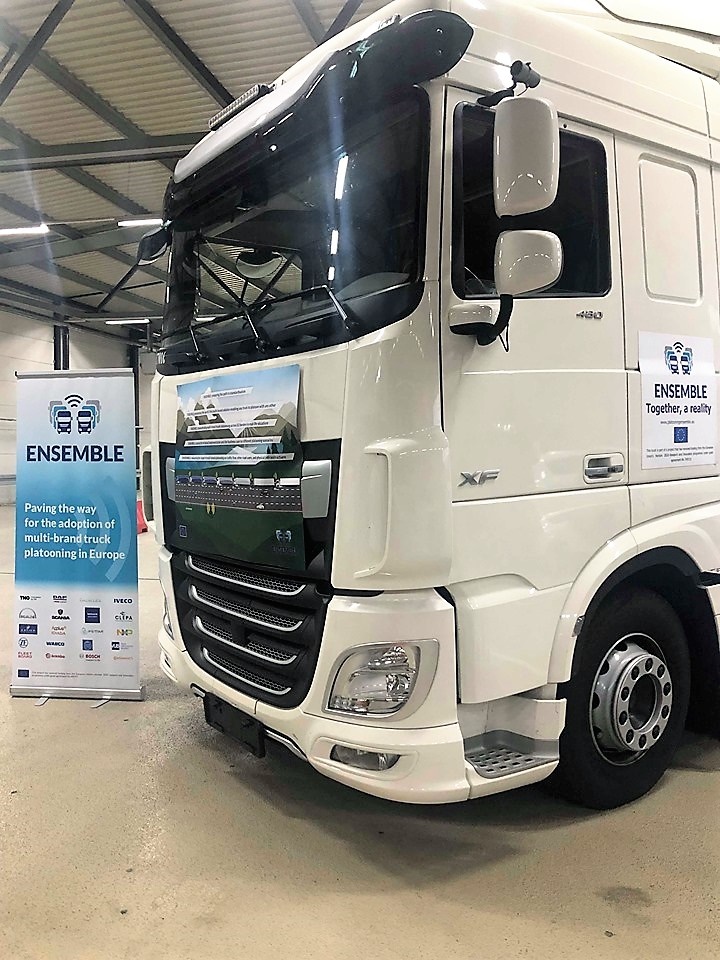
Over half way through is the EU’s €19.8 million ($21.8 million) ENSEMBLE project, led by Dutch independent research organisation TNO with Ertico - ITS Europe as a partner. This involves platoons of up to seven vehicles long moving across EU national boundaries. The 2018 German Electronic Drawbar - Digital Innovation (EDDI) project has demonstrated the beneficial effect that platooning can have on traffic capacity. The space needed for two trucks falls from around 90m to 50m – with three trucks the same figure is cut from 155m to 80m – with the improved traffic flow due to automated driving allowing more efficient use of the road infrastructure. The UK’s HELM platooning trial launched in August 2017. All three involve hauliers carrying genuine loads.
Phil Lloyd, head of engineering & vehicle standards policy at the UK Freight Transport Association, which is monitoring HELM, told ITS International: “Real-condition trials such as these are important because we need to know if truck platooning is going to be commercially viable. It may turn out not to be”.
One major advantage for the current generation of trials is that the major technological components needed – algorithms of the kind that are already being used in cargo bundling (where hauliers optimise available space on trucks, so avoiding empty return runs); the social internet (for communications); and the platooning equipment itself - are already available.
Economic issue
But a fundamental economic issue is affecting realistic expectations of take-up at this stage – and that is the fact that the large majority of European carriers are small- and medium-size enterprises (SMEs). For these the costs, both in initial investment and in managing the transactions carried out during operation, could outweigh the gains, argues European transportation economist Dr Wouter Verheyen of Rotterdam Erasmus University. The specialist in the crossroads of law and logistics has won a three-year fellowship grant to investigate the correct collaborative context for the deployment of platooning (as well as other emerging logistics technologies).
Verheyen is also a contributor to a recent compendium of current thinking on green logistics, Sustainable and Efficient Transport: Incentives for Promoting a Green Transport Market. He warns against drawing conclusions from existing material on ad hoc platooning – created when equipped trucks that are already on the road come across potential partners. He sees this as offering ‘very limited or even non-existent’ benefits.
One critical factor relevant to the ability of SMEs to take advantage of the new possibilities is the fact that the current price of the necessary platooning equipment is around €10,000 ($11,000) per truck (though this figure is expected to fall over the next few years). On this basis, Verheyen argues that trucks forming part of a three-vehicle platoon would need to travel for 223,773km (138,740 miles) before recouping the cost of their investment in the technology.
Given that the average European truck travels between 100,000km (62,000 miles) and 120,000km (74,400 miles) each year, this would mean taking around two years to achieve a return on the investment. (The calculation also leaves out the additional costs of driver training and equipment maintenance). A further point concerns the need for creating the high level of horizontal operational cooperation needed between SME hauliers, to make possible the sufficiently ‘thick cargo flows’ that will make platooning efficient for them and so accelerate its introduction across the industry, speeding up the delivery of environmental gains.
Once again, however, there is the fear that the costs of setting up and implementing the systems that will be needed to underpin such cooperation could outweigh the benefits.
Model contract
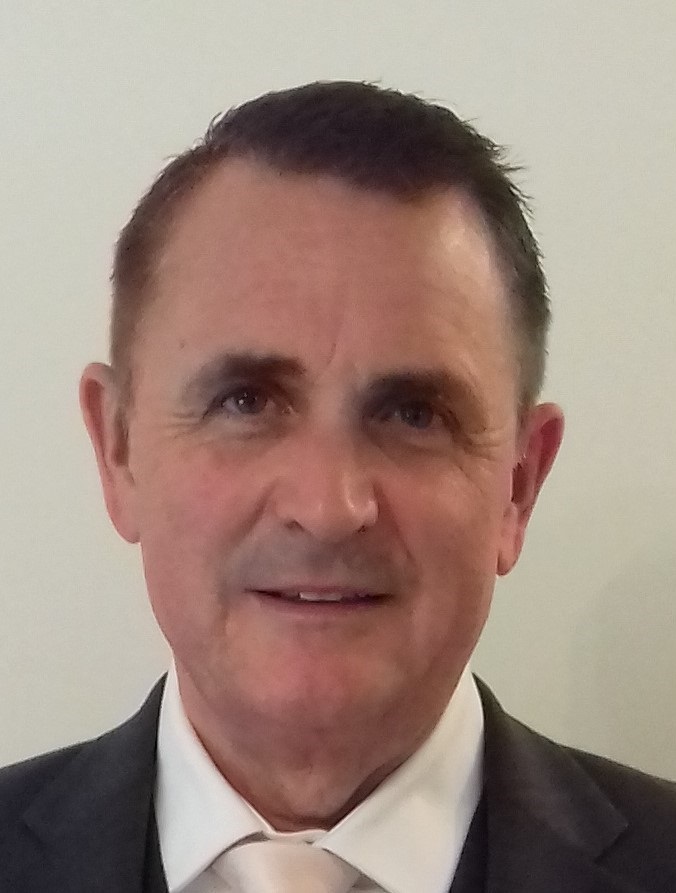
In a recent survey of European hauliers, 64% cited installation as an important factor in their decision-making process, while 36% named the administration. The most serious factor, however, concerned the uncertainty as to their level of exposure to liability for the goods being carried. 83% of respondents put this at the top of their list, with 38.8% rating it as a decisive issue. Issues needing to be resolved include failures by platoon member trucks to arrive at agreed meeting points on time, or even at all, so causing waiting period losses for other participants. Standstill costs per hour could range between €100 ($110) per hour for a two-truck platoon to €300 ($330) for a four-truck one.
In response, Verheyen highlights the need for the creation of a new general model contract for platooning, the achievement of the organisational and legal design which he identifies as the next key step needed in the platooning R&D process. Such a model could have wide applications across the logistics industry.
One area that he sees as benefiting from a combinatory approach involves the transportation costs of e-tailing. Products that consumers buy online and then decide to return as unsuitable cost web retailers money to retrieve. Bundling such shipments via joint collection points with other traders could result in savings in costs and kilometres driven, leading to worthwhile fuel savings and emissions.
Trucks in platoon | % savings truck 01 (leader) | % savings truck 02 | % savings truck 03 | % savings truck 04 | Average savings whole platoon |
2 | 5 | 15 | 10 | ||
3 | 5 | 20 | 15 | 13.33 | |
4 | 5 | 20 | 20 | 15 | 15 |
Buying in to emissions reduction
Another contributor to the green logistics research effort, Dr Suvi Sankari of the University of Helsinki, can see roles for consumers in influencing the levels of emissions that are generated in bringing retail products to buyers. She cites findings that as many as 35% could be green-minded enough to factor such data, incorporated into barcodes or labels, into purchasing decisions. Sankari accepts that the cost for manufacturers of making this more widely available is ‘a thorny issue’, although many companies at least record such information. The European Article Numbering system of unique product identification could offer a technical solution.