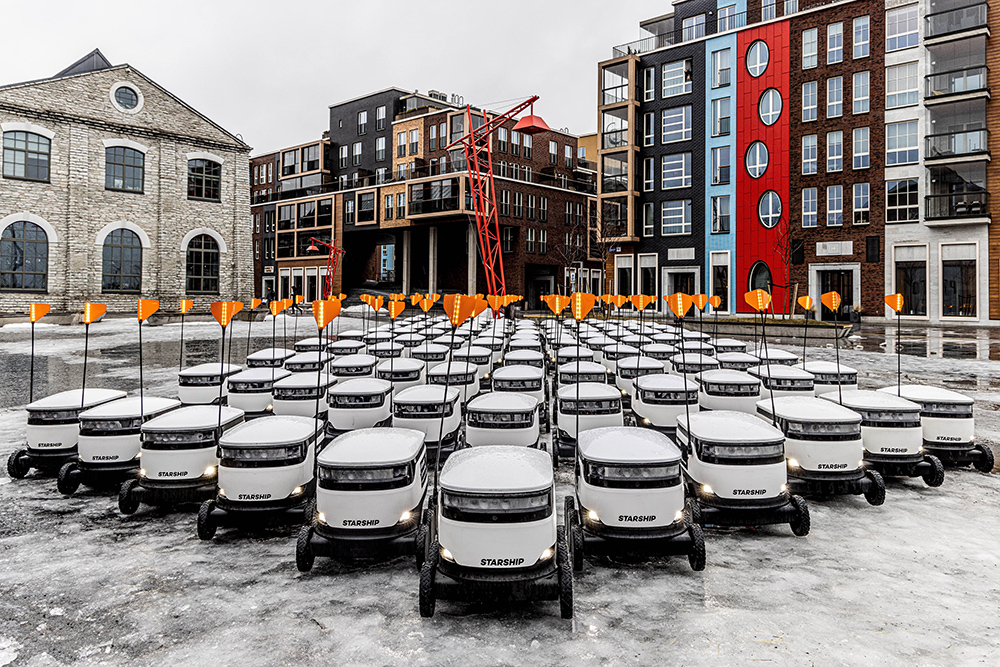
Personal delivery devices (PDDs) – or sidewalk robots – are an increasingly common sight in our cities. But four pilot schemes last year (see Special Delivery, ITS International November/December 2022, North America edition) highlighted some problems. In Pittsburgh, the bots found themselves unable to operate in a key neighbourhood “due to infrastructure limitations such as cracked sidewalks … sidewalk obstructions such as overgrown trees or bushes, or if cars were parked blocking the [way]”.
Difficulties in other cities weren’t any easier to solve. In Detroit, the PDDs had a hard time crossing a wide road on their route, with issues that can certainly be expected to show up in other cities: walk signals that were too short in duration; an inaccessible median. Meanwhile, some PDDs in San José got stuck (or even tipped over) when confronted with sidewalk obstructions, rendering themselves inoperable.
Engaging local communities in such projects as these is likely to become mandatory. According to David Rodriguez, co-founder of Kiwibot, whose machines took part in the trials, such engagements are important because they “allow people to adopt the technology more quickly, and accept the robots. It is essential to involve communities in local activities and events”.
Rodriguez cites one example: connecting with Miami’s Little Havana community by doing school activities. Rodriguez says: “This allowed people to feel safe around the robot. Thanks to Kiwibot’s technology, we could provide the city with data to identify where garbage was accumulating the most. With this data, the city could make decisions impacting citizens’ quality of life and solve health and wellness issues.”
Revolution and delivery
Kiwibot announced it would expand to 1,200 robots by the end of 2022 and now operates on around 25 US college campuses. The company has opened operations in the Middle East, while running pilots in Peru, Spain and Japan. In partnership with Sodexo, Kiwibot provides students, faculty and staff the opportunity to get their food or other goods delivered on-campus via app. Users then receive a unique link to track their order and follow the robot’s location in real time. The weight range of each Kiwibot is 20-29kg and, for safety, they run at human walking pace. Each robot creates a real-time virtual visualisation of the world by using sensors, reflective flags, night lights and a range Lidar. Kiwibots can stay centred on the sidewalk without any human assistance, which is what the company calls “C2C - Corner to Corner”.
Kiwibot insists its perception software is designed and programmed to ensure pedestrian safety. Campus or city mobility and foot traffic are taken into consideration in ways which serve customer needs safely, primarily by bots yielding the right of way. Kiwibots need teleoperators to cross the street - the scenario with the most risks – and the company obtains a permit signed by local and state authorities which allows its PDDs to transit private spaces and their surroundings. Hardware is designed and tested to handle extreme weather such as snow.
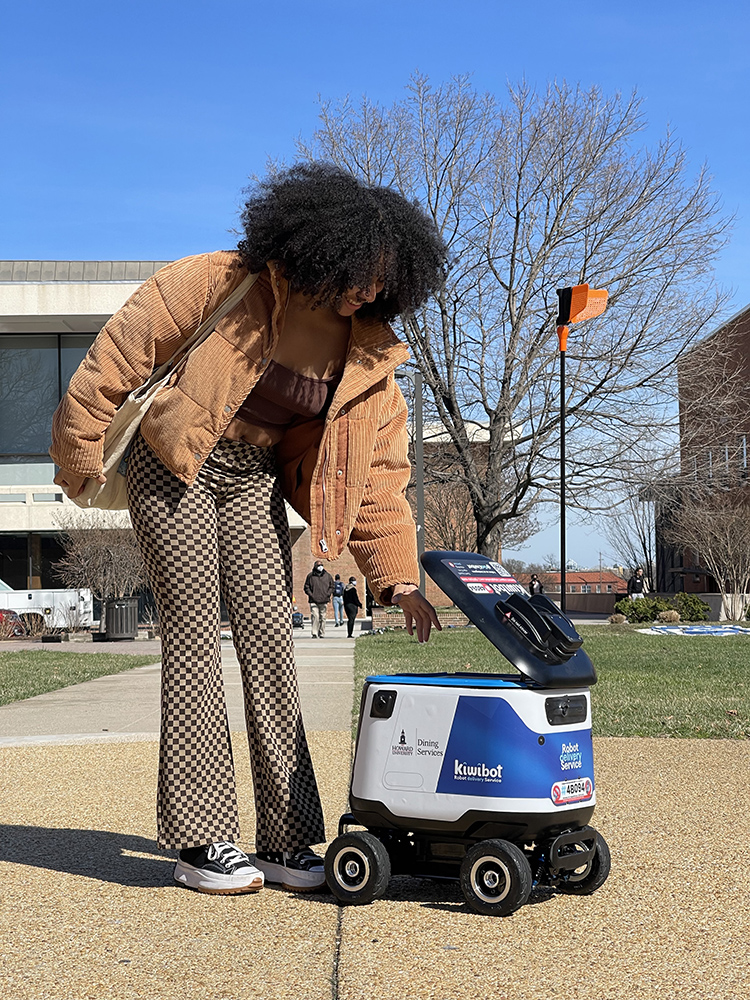
In addition to the company’s proprietary delivery service, Kiwibot has piloted mapping and off-campus advertising in US cities (including Pittsburgh, Boston, Washington DC, Detroit, Miami, and San José).
So how will PDDs make a real difference in the world of intelligent transport? “These robots have the potential to transform the way that last-mile delivery is conducted,” explains University of Michigan professor Ram Vasudevan.
“Current last-mile solutions contribute to large amounts of pollution and add to congestion. By utilising semi-autonomous, battery-powered robots that operate at the margin of the road and can get out of the way of traffic near the beginning and end of deliveries, these last-mile solutions could significantly improve accessibility.”
The race for space
Of course, Kiwibot is not the only start-up jostling for space on city sidewalks. Another is Starship Technologies, whose robots are designed to deliver food, groceries and packages locally in minutes. They have travelled millions of miles and completed 3.5 million autonomous deliveries around the world, the company says. Starship was founded by Ahti Heinla and Skype co-founder Janus Friis.
Thousands of the cooler-sized bots roam on sidewalks, interact with pedestrians and cross well over 100,000 roads per day. Inside each robot is a suite of sensors from optical systems, point cloud sensors, radars, inertial, ultrasonic sensors and processing units. The industry itself – and new sensors – are both developing rapidly and flexibility is at a premium.
Risto Meskus, Starship head of manufacturing and supply chain, explains that the firm designs, engineers and manufactures the robots in-house: “Manufacturing is co-located with the R&D team in Tallinn, Estonia, with a global supply chain. Parts are sourced mainly from Europe and China; electronics assembly and metal chassis are sourced from various factories around the globe”. The company puts together approximately 80% of the vehicles in-house with a manufacturing model which is relatively labour-intensive and divided into the following phases: body assembly, chassis assembly, final assembly and testing.
Developing and manufacturing complex products with cutting-edge technology requires a lot of agility from establishing a clear plan to take a product from concept to its final form to production and supply chain.
During the post-Covid supply chain disruptions, the company’s purchasing-and sourcing-related load increased 900% (including engineering impacts). However, Starship was able to make use of its vertical integration by redesigning tens of electronics subsystems to entirely different chip architectures, validating and testing the design and keeping growth at the target of 300% with what Meskus said was “minimal delivery disruptions and no system performance impact”.
As the company grows, Meskus points out that manufacturing and supply chain “continues to evolve” and his team is focused on developing solutions to enable further scaling. For instance, this includes transitioning a higher degree of sub-assembly value-add manufacturing to chosen contract manufacturers, “allowing in-house teams to focus on complex, high-value-add work content and driving manufacturability improvements in product design work”. In this way, Starship is actively working towards moving from building hundreds of units per month, to thousands.
The last mile
Nuro brings custom-designed electric PDDs to operate in local communities in three US states: Texas, Arizona and California. The goal which they promote is: “Less driving and more thriving”.
Nuro announced a $40 million investment to develop two new facilities in southern Nevada—an end-of-line manufacturing facility and world-class closed-course test track—to commercialise and scale production of what the company says is its third-generation autonomous vehicle.
Since enacting its first-in-the-US autonomous vehicle legislation in 2011, the state government of Nevada has been promoting itself to the world as a leader in promoting safe deployment.
Jiajun Zhu, Nuro co-founder and CEO, says this is a “significant moment” for the company. “Building on our tremendous momentum—including strategic partnerships with industry leaders such as Domino’s, Kroger and FedEx and operations in three states—we are now able to invest in the infrastructure to build tens of thousands of robots”.
Nuro will be taking over 74 acres of the Las Vegas Motor Speedway to build what it calls “a world-class, closed-course testing facility that will allow sophisticated development and validation of its autonomous on-road vehicles”. The testing track will measure bot performance in a broad range of scenarios, from avoiding pedestrians and pets to giving bicycles space on shared roadways, as well as environmental tests and vehicle systems validation.