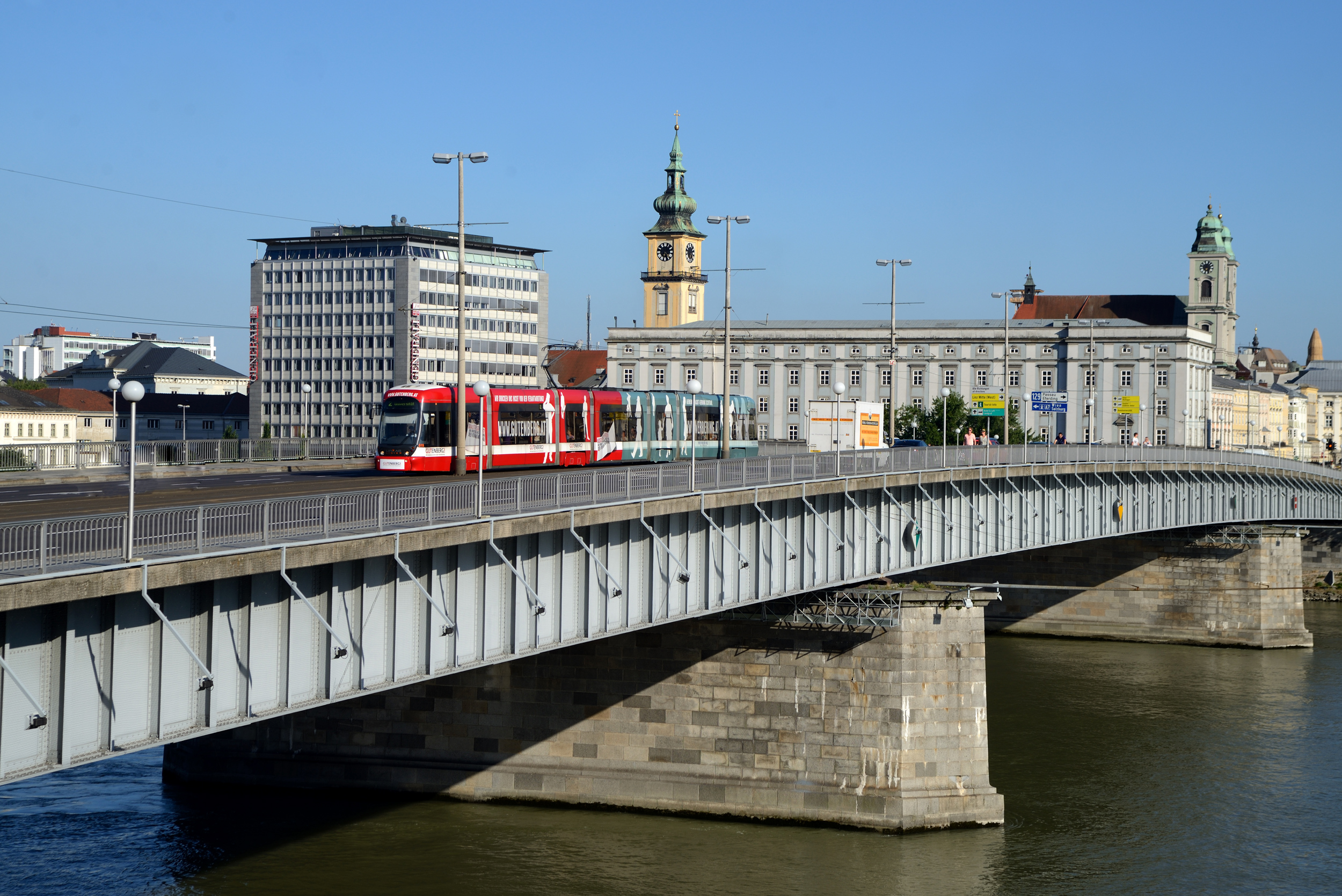
The new raft of sensor technology can provide cost savings as well as additional functionality, as David Crawford discovers.
Austria’s third-largest city, Linz, with a population of around 200,000, is recording substantial savings in its urban tram network within 18 months of introducing a new, high-technology approach to its public transport management. Tram, bus and trolleybus operator
Funded by the Austrian Climate and Energy Fund, this set out to deliver a sustained – and sustainable – increase in urban energy efficiency using targeted management technologies.
Projects already completed include the introduction of smart metering and cutting the costs of street lighting.
Trams form the backbone of the city’s public transport provision. So in May 2013, Linz Linien, which carries over 104 million passengers a year, joined forces with vehicle manufacturer
• Energy use reductions averaging 10.2%
• Sanding times down by 32 and 53%, reducing wheel and track wear
• Cost savings matching investment costs within one year
Here, too, the programme goal was to optimise energy usage in the 26.4km-long network. At the same time, it was to deliver additional benefits in the form of better operational performance, to be achieved via intensive data collection, communication and analysis.
Linz Linien operates three tram lines with a 4.4km-long extension of the existing Line 3 due to open in 2016. The first smart trams began running in September 2013, and have since achieved energy usage reductions averaging 10.2%, largely from more efficient heating, supporting the operator’s expectation that cost savings will match its investment within a year.
The project has equipped 23 out of its fleet of 56 Bombardier Cityrunner trams with sensors designed to monitor some 50 parameters, with the system taking readings at specified or event-driven intervals. An energy meter, plus current and voltage transformers, measure acceleration and braking energy; the return of regenerated braking energy to the power network; and the power consumption of auxiliary systems like heating, ventilation/air conditioning, door control and lighting. A rail transport-specific multifunction vehicle bus (internal component communications network) collects real-time data on the status of the tram’s traction controller, speed and temperature along with sanding events.
Detailed information on these enables close monitoring of the contribution of wheel-rail friction, and adhesion, to tram acceleration and braking. During the first four months of the pilot, aggregated sanding times fell by 32% while braking and 53% while accelerating, helping to reduce wear on wheels and tracks.
Stereoscopic cameras at the doors count passenger numbers, while excluding any personal data. The system provides real-time running information for specific trams and the occupancy of approaching ones, which can be integrated into smartphone apps for passengers’ benefit. One application envisaged for the vehicles’ satellite-based location technology is the ability to create geo-fenced speed limits, with deviations triggering safety alerts.
The onboard computer can store data locally for up to two days and transmits sensor data via an encrypted IP network to a Kapsch asset management platform for analysis with a view to reducing energy consumption and wear and tear. Each tram sends some 600MB per month in time-stamped data packets sent out at five second intervals over a 2.5G or 3G data connection.
Linz Linien’s control centre evaluates the incoming data via a web portal that enables integration into the operator’s existing IT infrastructure. Staff can use the system to contact the driver if necessary.
Johann Frisch, Linz Linien’s head of operations, depots and engineering, sees the greatest advantage of the smart tram as being the availability of relevant information in real time and at the right place. In its reporting, the system can integrate real-time information with historical data, to help with the identification of long-term trends. In this way it can, for example, help improve targeting of routine maintenance programmes by presenting accurate and more detailed information on a vehicle’s condition.
Kapsch operates the system’s reporting and analysis software, receiving a fee from Linz Linien for each equipped tram, and stores the resulting data in its own high-security data centre. The operator plans to have made its entire tram fleet ‘smart’ by the end-2015, by which time this will have grown by an additional six Cityrunners units ordered at a cost of €19 million (US$23.5 million).
Platooning involves a number of vehicles automatically following a manually-driven lead vehicle. Earlier this year, engineering consultancy
TRL’s chief research scientist and transportation research director Dr Alan Stevens and its senior human factors researcher Dr Nick Reed highlight that in controlled environments such as driverless trains and guided busways, automated driving technology is relatively mature. Sensors accurately perceive the traffic environment in real time, and platooning vehicles are typically equipped with multiple sensors such as radars and cameras.
Other components can include accurate, dynamically updated maps and precise positioning systems. Platoon vehicles typically combine these with vehicle-to-vehicle (V2V) communication technology, adaptive cruise control (ACC) and emergency braking systems to control vehicle position and spacing.
Steps towards on-road vehicle automation can already be seen in driver assistance systems such as adaptive cruise control, parking support and collision mitigation. Previous platooning projects in controlled conditions have demonstrated, demonstrated a range of benefits – particularly in fuel economy.
For example, the EU-funded
The performance of platooning in live road environments is not well characterised, so a road trial would be useful to ascertain the real-world benefits. However, Dr Stevens and Dr Reed point out that Government policymakers and legal experts must address a range of organisational, legal and human issues before full deployment.
From the statistical side Dr Stevens said the impact assessment data would need to account for the variations in loads, weather and seasonal conditions, driver and routes. These are important considerations in determining the overall size of the trial in terms of numbers of trucks and drivers and duration to achieve statistically meaningful results.
Important data would include real-time fuel economy figures via vehicle-derived data and paired comparisons with non-platoon vehicles as well as economic information on the benefits/disbenefits of vehicle rescheduling to participate in platoons. Video footage, or observer vehicles, would be needed to assess interactions with other road users along with ‘proxy’ data on measures related to safe driving conditions, for both platoon and non-platoon vehicles.
For his part Dr Reed said platooning drivers’ behaviour would need to be monitored to assess their attention to the driving task to ensuring that over-reliance on the system does not occur. The effectiveness of human-machine interface can be assessed using surveys of platoon drivers while the perception of platoons on the road can be derived from surveys of other road users.
The effect on vehicle wear and tear can be monitored via regular photographic recording and there would have to be a measurement of differences in road utilisation depending on the headways between vehicles.
In its conclusion the feasibility study found the technology is sufficiently advanced for trials to take place on live UK roads, given suitable preparation and safeguards. It further decided that this preparatory work is entirely feasible and can begin immediately.