ITS technology can do a great deal to improve tunnel safety, as Colin Sowman discovers. It was back in April 2004 that the European Parliament adopted the EU Directive which lays down the Minimum Safety Requirements for Tunnels in the Trans-European Road Network (2004/54/EC). This was the first unitary legislation setting minimum safety standards for European road tunnels and was designed to harmonise the management of tunnel safety at a national level. Operators of existing tunnels have until 30 April 201
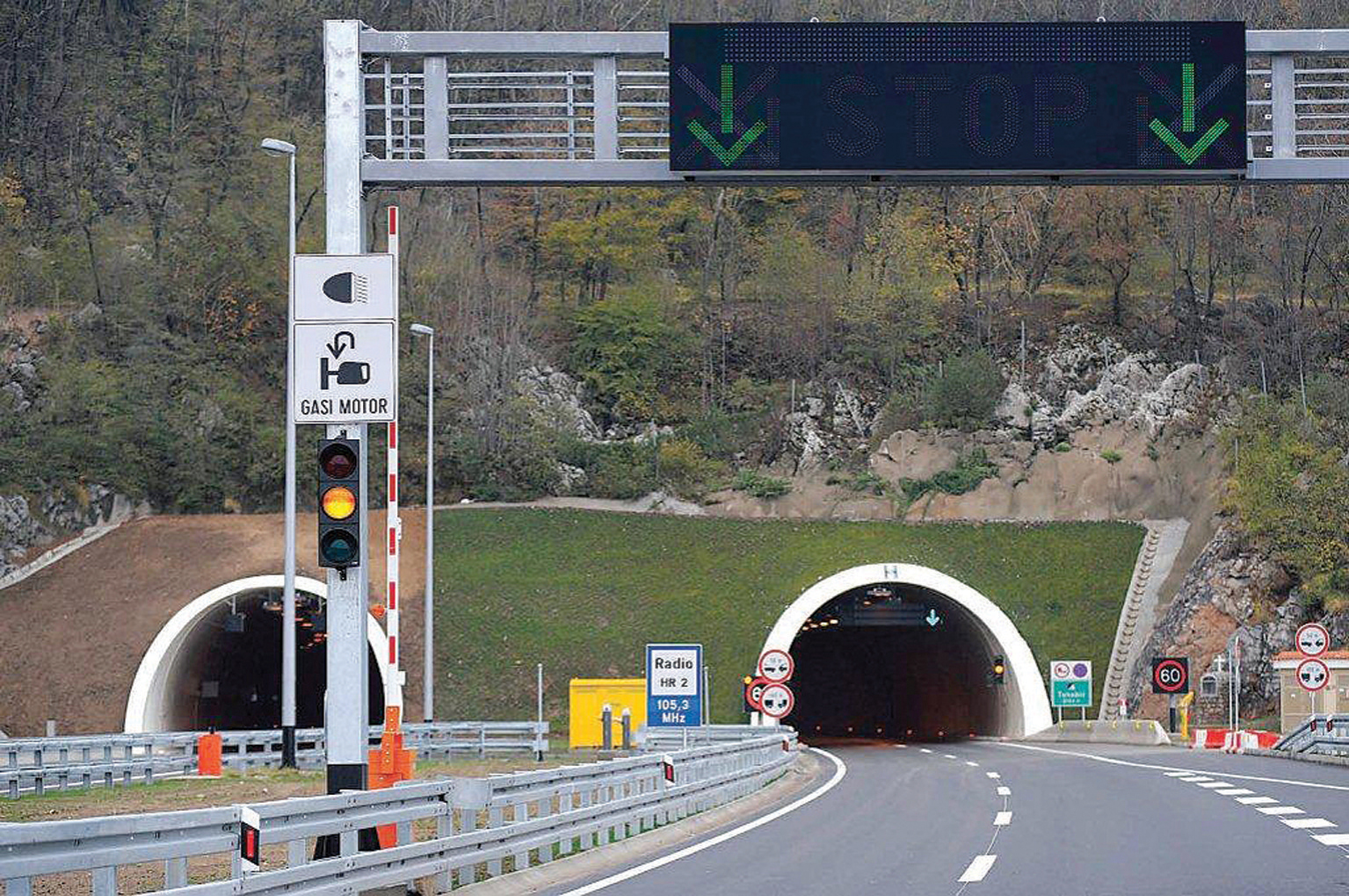
Tuhobić Tunnel entrance with lane control signs, radio frequencies and speed limit
ITS technology can do a great deal to improve tunnel safety, as Colin Sowman discovers.
It was back in April 2004 that the European Parliament adopted the EU Directive which lays down the Minimum Safety Requirements for Tunnels in the Trans-European Road Network (2004/54/EC). This was the first unitary legislation setting minimum safety standards for European road tunnels and was designed to harmonise the management of tunnel safety at a national level. Operators of existing tunnels have until 30 April 2014 to meet the regulations although in exceptional cases they may be given a further five years to comply.The standard covers tunnels of more than 500m in length that are part of the Trans-European Road Network (TERN), and new tunnels opened after 1 May 2006 had to comply from the day they opened. Every two years EU Member States must make a report to the EU Commission about the effectiveness of the facilities and measures in the affected tunnels.
According to Nicolas Adunka, project manager for the European Tunnel Assessment Programme (
While construction work is still in full swing in Europe’s tunnels as operators strive to meet the Directive’s deadlines by 2014, there are indications that individual EU Member States may require the full extension to 2019. “All the more reason for the EU to monitor the individual progress, consistently warn off any non-complying Member States and take adequate action in good time,” Adunka says.
Many tunnels have seen ‘dramatic improvements’ in their safety rating as judged by EuroTAP, which since 1999 has been run by the ADAC in co-operation with a dozen of European partner clubs. Moreover EuroTAP was supported by the
While a twin tube arrangement obviously provides opportunities for escape and rescue routes, having two bores is not a prerequisite of gaining an ‘acceptable’ EuroTAP rating. “Following the EU Directive, for a new tunnel with predicted traffic flows of 10,000 cars per day, two tubes will be necessary. But for existing tunnels, operators would have to consider the costs and benefits of all safety options including changes to the infrastructure,” says Adunka.
In this respect it is interesting to note that the combination of traffic surveillance and communications account for 28% of the marks in the EuroTAP evaluation. Other areas such as emergency management and fire protection account for a further 26% of the marks pushing the influence of ITS related functions beyond 50%.
Adunka says fire, or more specifically toxic smoke, is the biggest safety and health problem in tunnels for road users and therefore ventilation is one of the key considerations: “People need to get fresh air so the ventilation system must restrict the spread of smoke in the first 10 minutes of a fire otherwise they will be overcome by the toxic fumes and gases. A lot of thought has to go into the ventilation system and the control of the ventilation system. What needs to happen when there is a fire in a mountain tunnel may be very different to what is needed in a city tunnel.”
Beyond ventilation to enable people to survive, it must be a short distance to an emergency exit in modern tunnels and there must be emergency lighting to show travellers how to reach areas of safety. And there needs to be a way of preventing more vehicles entering the tunnel while enabling access for the emergency services. Practical measures such as escorting vehicles carrying dangerous goods or arranging dangerous goods loads to transit the tunnel late at night will also help reduce the impact on the public of any incident that might occur.
“Such measures can be very effective when there is no second tube. And even if there is a second tube, there still needs to be a way to get drivers and passengers safely to that second tube without exposing them to danger from other vehicles, fire or toxic smoke,” Adunka says.
The authorities in Croatia have upgraded the tunnels on the Rijeka-Zagreb motorway which forms part of the E-65 European road network and links the seaport of Rijeka to the Croatian capital Zagreb and beyond. The motorway (domestically known as the A6) is 146.50km long and has three notable tunnels at its western end: Tuhobi, Javorova Kosa and Veliki Glozac. In 2004 the Tuhobi tunnel was second to last in the overall EuroTAP ranking with a ‘very poor’ rating. Following the upgrade the tunnel was retested and received a ‘very good’ rating.
In the upgrade a second bore was added but, perhaps more importantly, so was an array of other safety equipment and measures starting with a Croatia-wide 100km/h speed limit in tunnels and a ban on trucks overtaking. There is now a control centre with uninterrupted video monitoring of entire 2.1km tunnel and a maximum distance between video cameras of 80m.
The system also has an automatic incident detection system to detect fire, smoke, carbon monoxide, stationary vehicles and obstacles, vehicles travelling the wrong way, vehicles in emergency lanes or lay-bys, pedestrians and congestion. All incidents are automatically archived.
The longitudinal ventilation system is designed to provide air flow greater than 3m/sec in the self rescue phase of an incident with the air (smoke) flow in the same direction as the traffic (although the fans are reversible).
There are emergency exits every 200m with fire resistance doors to protect against smoke intrusion. An emergency uninterruptible power supply (UPS) that feeds emergency lighting is positioned 1.5m above the pavement and the escape route signs (direction and distance to nearest exit) are located every 25m.
Illumination is provided throughout the tunnel. It has adaptation lighting in the first 200m and provides average luminance across the lane area inside the tunnel. This is backed up with emergency lighting to cover power failures which is powered via two independent lines from the UPS.
Emergency phones, also connected to the UPS, are positioned at 180m intervals and the tunnel operator’s staff, fire brigade, police and ambulance have access to uninterruptible tunnel radio. If an emergency telephone is used, an alarm is automatically activated initiating flashing lights inside the tunnel, the speed limit is reduced to 80km/h and the tunnel’s lighting system is brought up to full capacity.
There are loudspeakers throughout the tunnel and portals to communicate with motorists and passengers as well as traffic radio (including voice break-in) with the frequencies displayed inside and outside the tunnel. Mobile phones are able to send and receive inside the tunnel.
Heat resistant concrete with a special coating is used inside the tunnel as are heat resistant cables for safety-relevant items such as CCTV and heat imaging cameras. Fire extinguishers are positioned every 150-180m and alarms are automatically activated when a fire extinguisher is used as is the fire brigade alert and flashing light signal inside the tunnel. There is a manual fire alarm (push buttons) as well as a heat detection system and as soon as an alarm is triggered the lighting levels are automatically raised to maximum.
A pressurised firefighting water supply with a flow rate of 20litre/sec is available throughout the tunnel with the maximum distance between hydrants of 200m. Fire-fighting water is supplied from at least two points from a reservoir with a head of 150m. Every 50m there is a siphon into the drainage system has a maximum capacity of 160litre/sec and is designed to dispose of combustible or toxic liquids.
To minimise the risk of problems in the tunnel vehicles carrying dangerous goods have time slots in the quiet period between 23.00 and 05.00 and are escorted. There is also a vertical clearance check before the portals.
Less safety critical are systems for automatic congestion data collection and to prevent motorists entering a congested tunnel there are tunnel closure traffic lights and a physical barrier before the tunnel. Inside the tunnel there are further traffic lights and lane control signals
Adunka says the work done in the Tuhobi tunnel is an excellent example of how electronic systems and modern tunnel operation and management can enhance driver and passenger safety in tunnels. The categories, main parameters and methodology of the EuroTAP can be found on its website: %$Linker: