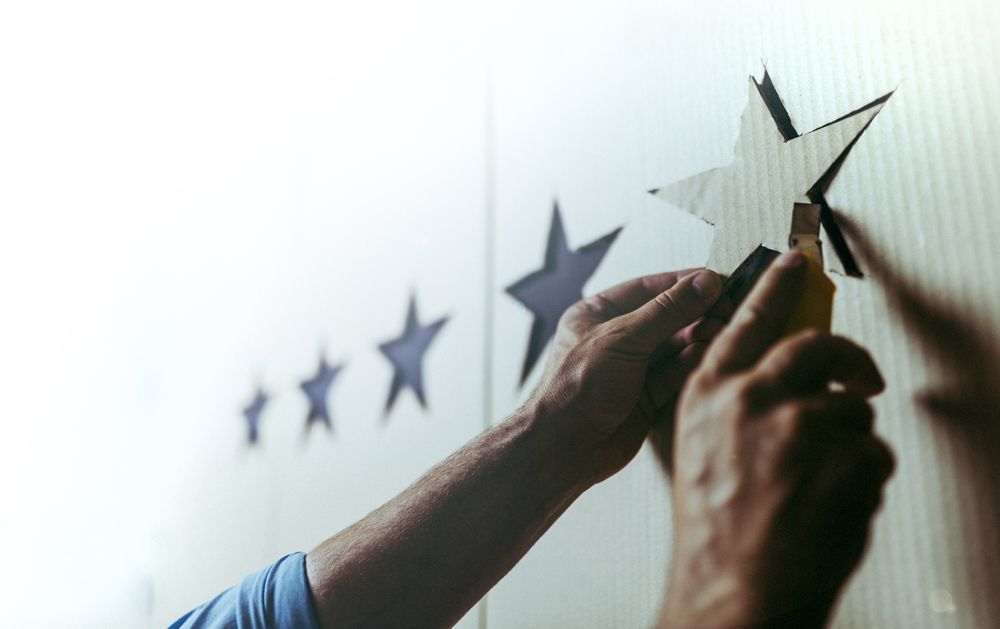
Embracing the principles of Lean Six Sigma, a company can employ methodologies proven to consistently and efficiently deliver a high level of service performance. It’s an approach that removes wasteful decision-making, maximises reliability, increases productivity, and focuses on continuous improvement. A Lean Six Sigma-based approach sets the benchmark for quality excellence through the application of systematic methods that provide measurable results - results that validate your services meet the gold standard for quality.
According to Shimmick’s director of operations and management, Rowdy Kemnitz: “An organization that centres their quality program around Lean Six Sigma principles mitigate risks associated with change and builds a culture that promotes ownership, efficiency, and improvement. To underscore our commitment to delivering quality across our operations, we certify our project supervisors and managers as Yellow and Green Belts, and our quality managers as Black Belts. You can’t just say you are committed to quality; you must demonstrate it. At Shimmick, we work with our clients in a proven, systematic manner to make quality and continuous improvement more than just a catchphrase."
Shimmick has over 25 years of experience in operating and managing toll systems, customer service centres, walk-in centres and manual lane collections. Delivering quality and continuous improvement based on Lean Six Sigma practices will result in improved processes and efficiencies for our clients, but most important, it delivers improved customer experiences for their customers.